The Complexity of Purchase Order Management
Supplier-logistics platform buy order management can be an intricate web. Suppliers must quickly fulfill orders with precise product specifications, quantities, and price. Logistics platforms manage shipping, deliveries, and inventories to ensure everything arrives on time and in the proper location.
This method gets messy when done manually. Outdated methods like emails, spreadsheets, and phone conversations cause confusion, lost orders, delays, and costly blunders. It's also time-consuming and laborious, so your staff spends more time on paperwork than on key business activity.
When purchase orders are misplaced or a vital step is skipped, supply chain delays cause irritation. Errors can proliferate across various parties and platforms, causing customer dissatisfaction, supplier tension, and operational issues.
If you're still manually processing purchase orders, you've likely experienced some common pain points.
- One lost signature or email can halt an order. The miscalculation causes missed deadlines and leaves suppliers and consumers in the lurch.
- Manually entering orders increases error risk significantly. A purchase order error, improper quantity, or misread direction can result in shipping the wrong things or nothing at all.
- Your order's status is nearly impossible to track without real-time updates. Calls and email status checks may be needed to confirm shipping.
- Suppliers and logistics platforms can use different systems, causing an integration gap. More manual input and double-checking are needed to coordinate orders across platforms due to this disparity.
- Purchase orders are manually managed, wasting hours that could be used to develop your business, improve customer service, or improve operations. This is unsustainable in today's fast-paced business world.
Automated Purchase Order Flows
Automated purchase order flows between suppliers and logistics platforms can revolutionize the way you manage your supply chain. Instead of juggling emails, phone calls, and spreadsheets, automation connects all your systems and processes into one seamless flow.
With automated purchase order flows, your orders move from request to fulfillment without manual intervention, drastically reducing the risk of errors and speeding up the entire process. Here's how it works:
- An automated system generates a purchase order and sends it to the supplier once a customer places an order, following rules and approval protocols. Multiple approvals needed before order processing? Automation handles it too. Everything is organized and trackable—no lost emails or late signatures.
- Real-time updates from automation keep suppliers and logistical personnel informed. This means order or delivery schedule changes are conveyed quickly. All parties know what's happening and when shipments will arrive.
- Automating the procedure greatly reduces human error. We automatically fill in purchase order details, gather data from appropriate sources, and notify you if anything seems odd. Instead than entering in the numbers or checking everything, automation does it.
- Automated flows link with supplier and logistics platforms to ensure accurate, timely, and coordinated orders. Automation updates everything, from ERP data to inventory management system sync. Stop double-entering or cross-referencing data between systems.
- Automation expedites orders from placement to delivery. By reducing manual processing, approval bottlenecks, and communication problems, you streamline product flow in your supply chain. Customer satisfaction and supplier relations improve with faster fulfillment.
- Automated purchase order flows scale with your business, whether you process 10 or 10,000 orders daily. Automation seamlessly handles growing workloads, letting your team focus on strategic efforts instead of tedious activities.
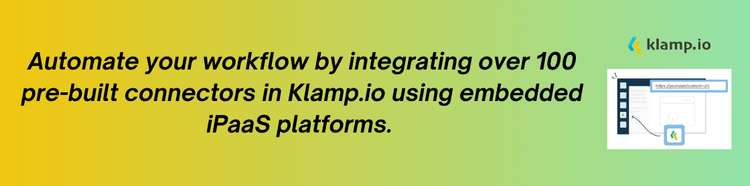
Automated purchase order flows eliminate manual process inefficiencies and frustrations. Automation with Klamp helps you stay ahead, strengthen supplier relationships, and satisfy consumers with real-time communication, decreased errors, and speedier fulfillment.